


ABOUT US
A Shared Vision
Janki Newsprint Pvt. Ltd. began as a humble vision shared by Lt. Sh. Ravi Prakash Garg, Mr. Anand Prakash Garg, and Mr. Ashok Garg. In 2000, with unwavering determination and a production capacity of just 50 MT daily for writing, printing, and newsprint, they set out on a journey to revolutionize the paper industry. Today, through relentless hard work and a commitment to excellence, we have expanded our capacity to an impressive 450 MT daily. This remarkable growth is a testament to our founders' legacy and our ongoing dedication to innovation and sustainability.
Janki Newsprint Pvt. Ltd. operates three highly successful paper manufacturing machines, producing SS Craft, Light Gram Kraft, Unbleached Paper, MG Poster, and Tissue. Our in-house power generation plant features a 55 TPH boiler and an 8 MW turbine to meet our steam and power requirements.
Janki Newsprint is a completely recycled-based paper manufacturing industry. Initially, the company was known as Sumit Agro Ltd., but in 2010, it was re-registered as Janki Newsprint Pvt. Ltd. In our first paper plant, we produced writing, printing, and newsprint paper. However, in 2012, we converted this machine to produce SS Kraft Paper.
In 2007, we launched a new paper manufacturing plant with a capacity of 150 MT, supported by an in-house power generation facility with a 24 TPH boiler and a 3 MW power plant. In 2021, we started our new Yankee Paper Manufacturing Plant, which includes a 55 TPH boiler and an 8 MW power plant. Today, we manufacture 450 MT of paper daily.

OUR CLIENTS
We Believe Every Client Is a Valuable Long-Term Partner








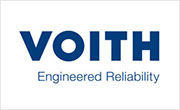

OUR CLIENTS
We Believe Every Client Is a Valuable Long-Term Partner





OUR CLIENTS
We Believe Every Client Is a Valuable Long-Term Partner





OUR MANUFACTURIGN PROCESS
Process with Sustainability at its Core
Collection & Transportation
Often, a paper stock dealer or recycling center will collect recovered paper from homes, schools, or offices. At the recycling center, the collected paper is wrapped in tight bales and transported to our paper mill, where it is recycled into new paper.
Storage and Sorting
Our workers unload the recovered paper and store it in warehouses until needed. Successful recycling requires clean recovered paper, so we ensure our paper is free from contaminants such as food, plastic, metal, wax, and other trash that can make paper difficult to recycle. Moreover, the paper is sorted into different grades, such as newspapers, duplex, white cuttings, scan boards, and old books, to suit different layers of paper products. We use various grades of recovered paper to manufacture different types of recycled paper products. Finally, forklifts move the paper from the warehouse to large conveyors for processing.
Re-Pulping & Screening
The paper is transported by conveyor to a large vat called a pulper, which contains water and chemicals. The pulper chops the recovered paper into small pieces. Heating the mixture breaks the paper down more quickly into tiny strands of cellulose (organic plant material) called fibers. Eventually, the old paper turns into a mushy mixture known as pulp. The pulp is then forced through screens with holes and slots of various shapes and sizes. These screens remove small contaminants such as bits of plastic and globs of glue. This process is known as screening.
Cleaning
Our mill then cleans the pulp by spinning it in large cone-shaped cylinders. Heavy contaminants, such as staples, are thrown to the outside of the cone and fall through the bottom of the cylinder. Lighter contaminants collect in the center of the cone and are removed. This process is known as cleaning.
Refining & Bleaching
During refining, the pulp is beaten to make the recycled fibers swell, making them ideal for papermaking. If the pulp contains any large bundles of fibers, refining separates them into individual fibers. If the recovered paper is colored, color stripping chemicals remove the dyes from the paper. This process is mainly done to increase the freeness of pulp in water.
Papermaking
Now, the clean pulp is ready to be transformed into paper. The pulp is mixed with water and chemicals to create a mixture that is 99.5% water. This watery pulp mixture enters the headbox, a large metal container at the beginning of the paper machine, and is then sprayed in a continuous wide jet onto a massive flat wire screen that moves rapidly through the paper machine. On the screen, water begins to drain from the pulp, and the recycled fibers swiftly bond together to form a watery sheet.
The sheet progresses quickly through a series of felt-covered press rollers, which extract more water. As the sheet progresses, it starts to resemble paper. It then passes through a series of heated metal rollers that dry the paper. Finally, the finished paper is wound onto a large roll and removed from the paper machine.
The paper roll is then cut into smaller rolls or sometimes into sheets before being transported to a converting plant. At the converting plant, it will be printed or transformed into various products such as envelopes, paper bags, or boxes.